Maximizing Efficiency and Performance A Comprehensive Guide to Work Truck Fuel Tanks
Introduction
Work trucks play a crucial role in various industries, from construction and agriculture to transportation and logistics. These vehicles are relied upon for their durability, power, and versatility in carrying out a wide range of tasks. However, one of the most critical components of a work truck that often goes unnoticed is the fuel tank. The fuel tank is the heart of the vehicle, providing the necessary energy to power the engine and keep the truck running efficiently. In this comprehensive guide, we will delve into the world of work truck fuel tanks, exploring their types, sizes, materials, maintenance, and best practices to maximize efficiency and performance.
compressed garbage truck of Work Truck Fuel Tanks
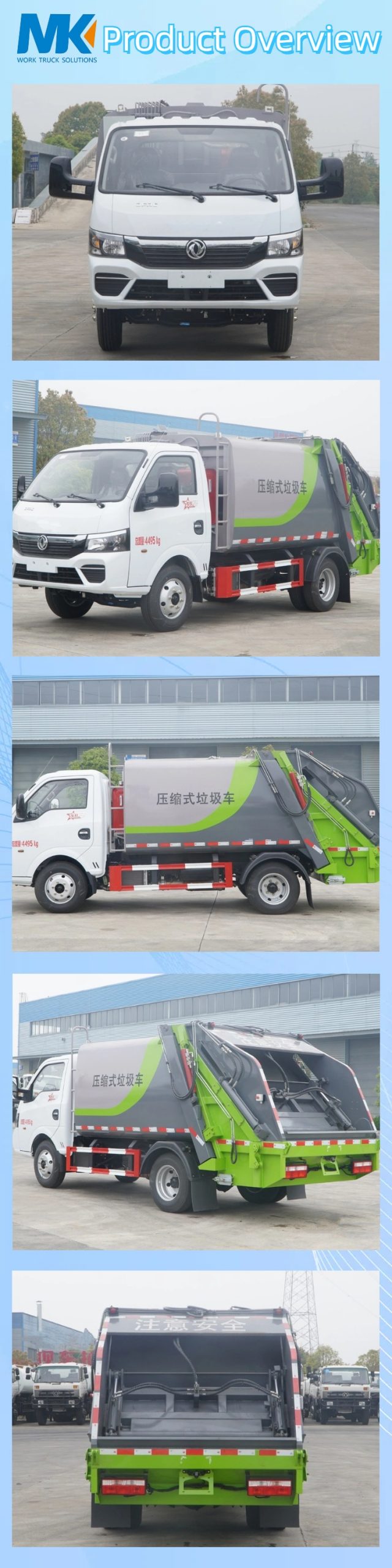
Work truck fuel tanks come in various types, each designed to meet specific needs and requirements. The most common types of fuel tanks for work trucks include:
1. Standard Steel Tanks: Standard steel tanks are the traditional choice for work trucks due to their durability and reliability. These tanks are made of high-quality steel and are designed to withstand rough conditions and heavy use. Standard steel tanks are available in different sizes to accommodate varying fuel capacities.
2. Aluminum Tanks: Aluminum tanks are becoming increasingly popular in the work truck industry due to their lightweight construction and corrosion resistance. Aluminum tanks offer a weight-saving advantage, which can result in improved fuel efficiency and payload capacity. They are also less prone to rust and can last longer than steel tanks.
3. Auxiliary Tanks: Auxiliary tanks are additional fuel tanks that can be added to work trucks to increase the vehicle's fuel capacity. These tanks are commonly used in long-haul trucks or vehicles that require extended range. Auxiliary tanks can be mounted in various locations, such as the bed of the truck or underneath the chassis, to maximize fuel storage without compromising space.
4. Transfer Tanks: Transfer tanks are designed for transferring fuel from one vehicle to another or for refueling equipment on the job site. These tanks are equipped with pumps, hoses, and nozzles for easy dispensing of fuel. Transfer tanks are commonly used in industries such as construction, agriculture, and landscaping, where on-site refueling is necessary.
5. Combination Tanks: Combination tanks combine fuel and other fluids, such as hydraulic oil or diesel exhaust fluid (DEF), in a single unit. These tanks are ideal for work trucks that require multiple fluid storage options in a compact design. Combination tanks help optimize space utilization and streamline fluid management on the job site.
Sizes of Work Truck Fuel Tanks
Work truck fuel tanks are available in a range of sizes to accommodate different fuel capacities and vehicle requirements. The size of the fuel tank plays a crucial role in determining the vehicle's range, fuel efficiency, and operational flexibility. Common sizes of work truck fuel tanks include:
1. 20-30 Gallons: Work trucks with smaller fuel requirements, such as light-duty pickups or vans, typically have fuel tanks ranging from 20 to 30 gallons. These tanks are suitable for short-distance travel and light-duty applications where frequent refueling is feasible.
2. 40-60 Gallons: Medium-duty work trucks, such as utility trucks or delivery vehicles, often feature fuel tanks with capacities between 40 and 60 gallons. These tanks provide a balance between fuel capacity and vehicle weight, making them ideal for daily use in urban or suburban settings.
3. 70-100 Gallons: Heavy-duty work trucks, including dump trucks, tow trucks, and tractor-trailers, require larger fuel tanks ranging from 70 to 100 gallons or more. These tanks are designed to support long-haul operations and high fuel consumption rates typical of heavy-duty vehicles.
4. Custom Sizes: In some cases, work truck operators may require custom-sized fuel tanks to meet specific operational needs. Custom-sized tanks can be fabricated to fit unique vehicle configurations or space constraints, providing a tailored solution for specialized applications.
Materials of Work Truck Fuel Tanks
The materials used in work truck fuel tanks play a significant role in determining the tank's durability, weight, and resistance to corrosion. The most common materials used in work truck fuel tanks include:
1. Steel: Steel is a traditional material for fuel tanks due to its strength and durability. Steel tanks are resistant to impact damage and provide reliable fuel storage for heavy-duty applications. However, steel tanks are prone to rust and can add significant weight to the vehicle.
2. Aluminum: Aluminum is a lightweight and corrosion-resistant material that offers several advantages for work truck fuel tanks. Aluminum tanks are ideal for applications where weight savings and fuel efficiency are priorities. Although aluminum tanks may cost more upfront, they can provide long-term benefits in terms of durability and performance.
3. Plastic: Plastic or polymer fuel tanks are gaining popularity in the work truck industry due to their lightweight construction and resistance to corrosion. Plastic tanks are easy to install, cost-effective, and offer excellent chemical resistance. However, plastic tanks may not be as durable as steel or aluminum tanks and can be susceptible to impact damage.
4. Composite: Composite materials, such as fiberglass or carbon fiber, are used in high-performance work truck fuel tanks that require exceptional strength and weight savings. Composite tanks are lightweight, durable, and resistant to corrosion, making them ideal for specialized applications where performance is paramount.
Maintenance of Work Truck Fuel Tanks
Proper maintenance of work truck fuel tanks is essential to ensure optimal performance, prevent fuel leaks, and prolong the tank's lifespan. Regular inspection and maintenance practices can help identify potential issues early and address them before they escalate. Here are some key maintenance tips for work truck fuel tanks:
1. Inspect for Leaks: Regularly inspect the fuel tank and fuel lines for any signs of leaks, corrosion, or damage. Leaks can lead to fuel loss, environmental contamination, and safety hazards. Address any leaks promptly by repairing or replacing damaged components.
2. Check Mounting Hardware: Ensure that the fuel tank is securely mounted to the vehicle chassis using the appropriate hardware. Loose or damaged mounting brackets can cause the tank to shift or vibrate, leading to premature wear and potential leaks. Tighten or replace mounting hardware as needed.
3. Clean the Tank Interior: Periodically clean the interior of the fuel tank to remove sediment, debris, or contaminants that can affect fuel quality. Use a tank-cleaning solution and a fuel tank brush to scrub the interior surfaces and rinse thoroughly with clean fuel before refilling.
4. Monitor Fuel Quality: Monitor the quality of the fuel stored in the tank to prevent contamination or degradation. Use fuel additives or stabilizers to maintain fuel freshness and prevent water accumulation. Regularly test the fuel for water content, particulate matter, or microbial growth.
5. Inspect Fittings and Seals: Check the fittings, hoses, and seals connected to the fuel tank for signs of wear, cracks, or leaks. Replace any damaged components to prevent fuel leaks or vapor emissions. Use high-quality fittings and seals compatible with the fuel type stored in the tank.
6. Maintain Ventilation System: Ensure that the fuel tank ventilation system is functioning correctly to prevent pressure buildup or vacuum conditions inside the tank. Blocked vents can lead to fuel tank collapse or expansion, affecting fuel flow and engine performance. Clean or replace vent components as needed.
Best Practices for Maximizing Efficiency and Performance
In addition to regular maintenance, there are several best practices that work truck operators can implement to maximize fuel efficiency and performance of the fuel tank:
1. Optimize Route Planning: Plan routes efficiently to minimize idle time, reduce unnecessary mileage, and avoid traffic congestion. By optimizing route planning, work trucks can conserve fuel, reduce emissions, and improve overall productivity.
2. Maintain Proper Tire Pressure: Keep tires inflated to the recommended pressure levels to reduce rolling resistance and improve fuel efficiency. Underinflated tires can increase fuel consumption and accelerate tire wear, impacting both performance and safety.
3. Avoid Excessive Idling: Minimize idle time by turning off the engine when the work truck is stationary for extended periods. Excessive idling consumes fuel unnecessarily and contributes to increased emissions. Use auxiliary power units or engine block heaters to maintain cabin comfort without idling.
4. Use Fuel-Efficient Driving Techniques: Encourage drivers to adopt fuel-efficient driving techniques, such as smooth acceleration, steady speed, and anticipation of traffic conditions. Aggressive driving behaviors, such as rapid acceleration and hard braking, can decrease fuel efficiency and increase wear on the vehicle.
5. Monitor Fuel Consumption: Track fuel consumption rates and compare them to vehicle performance metrics, such as distance traveled and load weight. Identify trends or anomalies in fuel usage to detect potential issues, such as engine inefficiencies or fuel leaks, and take corrective action promptly.
6. Invest in Fuel Management Systems: Consider installing fuel management systems in work trucks to monitor fuel levels, track usage patterns, and optimize fuel efficiency. These systems can provide real-time data on fuel consumption, route efficiency, and driver behavior to help operators make informed decisions.
Conclusion
Work truck fuel tanks are essential components that play a critical role in powering the vehicle and supporting daily operations. By understanding the types, sizes, materials, maintenance practices, and best practices for work truck fuel tanks, operators can maximize efficiency, performance, and longevity of their vehicles. Whether using standard steel tanks, aluminum tanks, auxiliary tanks, or combination tanks, work truck operators can benefit from proper maintenance and proactive measures to optimize fuel storage, reduce costs, and enhance operational productivity. Implementing a comprehensive approach to work truck fuel tank management can lead to improved sustainability, reliability, and overall success in various industries that rely on these versatile vehicles.